Not long ago, it seemed too futuristic to calculate life spans of industrial equipment under a variety of scenarios in real time. Today, it's not only possible, but it's also changing the way manufacturing works. By integrating cloud capabilities with the industrial Internet of Things (IoT), digital twinning can be achieved, allowing experimentation with variables in real time to predict outcomes.
What is a digital twin? In essence, it's a computer program that takes in real-world data about a physical object or system as inputs and produces simulations of how it will be affected by changes in those inputs.
For the third year in a row, Gartner (NYSE: IT), a research and advisory firm, has identified digital twinning as one of the top 10 strategic technology trends. According to Gartner, 13% of organizations that are implementing IoT have already adopted digital twins, and 62% are in the process or plan to do so. Gartner predicts a tipping point in 2022 when two out of three companies will have deployed at least one digital twin to optimize some facet of their business processes.
Digital twins can make smart factories even smarter
Digital twins can help equipment operators anticipate breakdowns, refining maintenance timing and reducing unexpected maintenance shutdowns, thereby dramatically lowering costs. The process is a simulation that allows engineers and designers to create virtual replicas of physical systems and devices, then introduce variables such as temperature, speed, and pressure. Digital twinning is different from creating a computer aided design (CAD) model in two ways: its connectivity and its variance.
For example, General Electric (NYSE: GE) aircraft engine digital twins combine sensor, performance, and environmental data with historical data from similar engines. The digital twin can then predict the life span of various engine components under different scenarios. This enables teams to make informed maintenance decisions, resulting in reduced turnaround time, greater safety, and lower costs.
In December 2019, Microsoft's (MSFT -1.73%) Azure IoT cloud system agreed to partner with engineering simulation company ANSYS (ANSS -0.13%) to provide physics-based digital twinning to industrial clients.
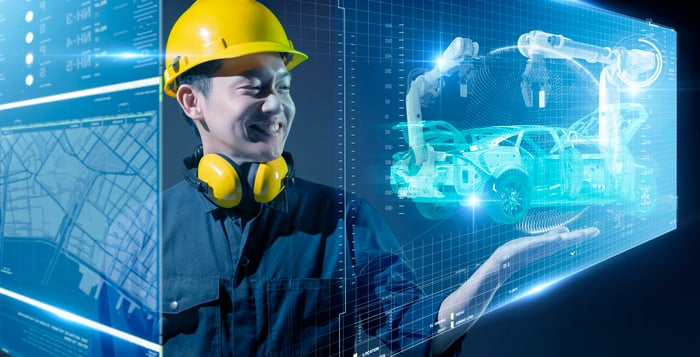
Image Source: Getty Images
Headquartered in Pennsylvania, ANSYS has 50 years' experience in simulation engineering, and specializes in 3D design software and modeling systems. Its advanced simulations in digital twinning can streamline automation and engineering processes.
The partnership between Microsoft and ANSYS integrates complementary systems for creating digital twinning. ANSYS leverages its proprietary Twin Builder solution across Microsoft's Azure IoT services to provide customers the most advanced simulation potential with the smoothest cloud interconnectivity.
Unlike more traditional virtual designs, like those from CAD, digital twins can be tested alongside the physical systems they're mirroring, and they allow engineers to perform predictive maintenance and test for faults before they have a chance to arise.
The Microsoft and ANSYS product is not the only one of its kind. Other partnerships are being formed as a number of companies begin to adopt digital twins into engineering and manufacturing systems. Rockwell Automation's (ROK -1.15%) Digital Partner Program helps industrial clients to optimize manufacturing. Microsoft and ANSYS are included in Rockwell's Partner Program, along with Accenture (ACN -1.18%); PTC (PTC -0.76%); and EPLAN, part of the German family business Friedhelm Loh Group.
Is digital twin technology a game changer for investors?
A MarketsandMarkets report updated in January estimates that the digital twinning market had a value of $3.8 billion in 2019, and will reach $35.8 billion by 2025, at a compound annual growth rate (CAGR) of 45.4%.
As often happens with new technology, many companies are unclear about the economic benefits and investments involved. Calculating the advantages of digital twinning can be daunting, further complicating adoption of the technology.
But the financial losses incurred by downtime in manufacturing can motivate executives to look closer at digital twinning. For instance, for CNH Industrial (NYSE: CNHI), which manufactures power trains and agricultural, industrial, and commercial vehicles, a minute of downtime can cost more than $160,000. The deployment of digital twinning identified the most crucial areas and helped CNH reduce expensive downtime and streamline operations.
Regarding digital twinning, Microsoft CEO Satya Nadella said:
Anybody who has a digital twin is able to first remote the control plane, is able to automate, is able to simulate. That's huge for anybody who is into manufacturing or is trying to model out and plan their supply chain. So I think that there are ways for us to participate in what ultimately will be productivity growth. But our immediate term, we are mostly building out the relationships, adding new customers, adding intensity in usage in existing relationships, which all in the long term will play out in terms of economics for us as well.
As Nadella pointed out, relationship-building with potential customers is underway, and groundwork is being laid for sales through education. The digital twinning partnership between Microsoft and ANSYS brings together powerhouses in cloud and engineering simulation. Digital twinning is affecting nearly every corner of the world, and manufacturing is leading the way as an early adopter.
Microsoft and ANSYS are well positioned as manufacturing disrupters offering digital twinning technology. Investors should carefully watch if widespread adoption occurs; these two companies, and share prices, could be powered forward on a wave of technological change.